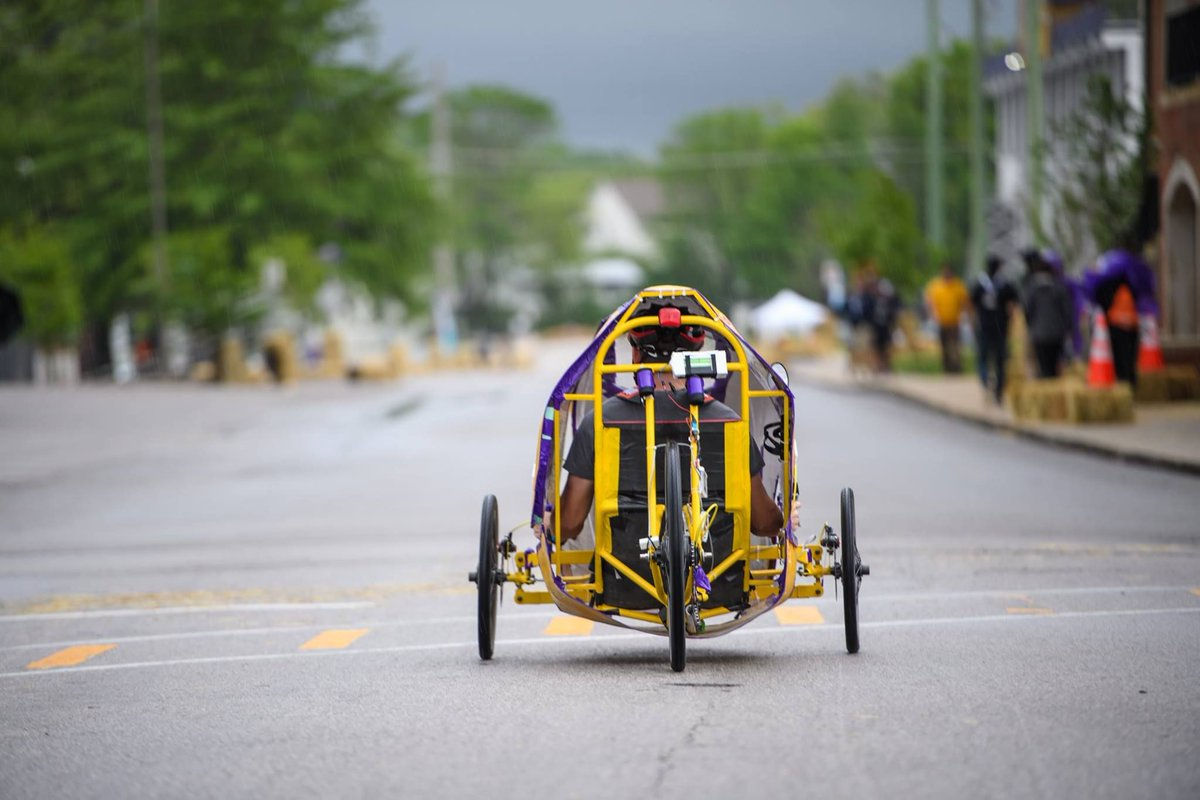
To achieve our goal of placing 3rd overall in the 2018 ASME HPVC West, the team has selected designs that ensure safety and produce a vehicle capable of strong performance. Different decisions involving all three subsystems of the vehicle were made in regards to designs that would uphold our standard of safety while simultaneously being innovative. To ensure the team manufactures a mechanically sound vehicle that would excel in competition, four objectives were created for the project. They are as follows:
​
-
Build a vehicle that is safe.
​
The ASME HPVC comes with a set of rules and regulations that are placed not only to make the competition fair, but to make it safe as well. To accomplish the first objective, the team will adhere to every safety requirement set by the competition. This includes, but is not limited to, having a roll cage attached to the frame, implementing a safety harness, and more. In addition to having features of the vehicle that adhere to the rules, the frame itself must be able to withstand top load of 600 lbs. and a side load of 300 lbs. The team plans to use a combination of Finite Element Analysis (FEA) and physical load testing to ensure the vehicle can withstand the forces required and more.
​
-
Build a vehicle that performs well.
​
The second objective stems from knowledge obtained from previous "Ke Koa" teams. Shortcomings that occurred in previous years, such as failed welding and poor turning radii, have been noted by the team and current ideas are being implemented to ensure they don't repeat. Stronger material that is easier to weld, such as steel, has been pitched as an idea for the vehicle's frame and a new steering system has been proposed to fix the problems that last year's indirect steering brought along. The ideas and designs done by previous "Ke Koa" teams that have worked in the past were also taken into consideration, being brought forth into our own ideas to either reuse or improve upon them. Ideas, such as using a recumbent tadpole styled tricycle, that have shown promise for past teams are being reworked with our team in the hopes to make a good thing better. More information about the design decisions can be viewed in the subsequent subsystem pages.
​
-
Build a vehicle that is marketable.
​
One purpose of the ASME HPVC that is emphasized is the development of vehicles that could be implemented by consumers of the future. It would not be enough to simply manufacture a vehicle that could win competition, but it must also be functional in a real world setting. The HPVC emphasizes this by designing the challenge to be within an urban setting. This pushes engineers to design vehicles that could be practical for the every day commuter, where traffic stops, road bumps, and pothole riddled roads could be obstacles seen on a daily basis.
With this in mind, and the fact that the innovation event is worth more points in the challenge than previous years, the team decided to design and manufacture an urban vehicle that can be stored in a variety of settings. To do this, a foldable frame was proposed as the main innovation. A hinge in the middle of the frame will be utilized as the folding point, allowing the vehicle to theoretically halve its length. It is with this innovation that the team hopes to win the innovation event with as, not only has a foldable vehicle with a full fairing not been seen in previous competitions, but the implications of its use in urban society would be beneficial. The ability to park the vehicle like a regular recumbent bike or fold it up and store in into a smaller space would make it a vehicle that a variety of consumers could use.
​
-
Build a vehicle that is easy to manufacture.
​
In order to accomplish the objective of making the vehicle easy to manufacture, certain decisions on the materials to be used, the shape of the vehicle's frame, the way to manufacture the fairing, and so much more had to made. With so many decisions to be made, the team split up into three different subsystems: the frame, the drivetrain, and the fairing. Each subsystem came up with a variety of micro-subsystems that dealt with the certain design decisions. Pros and cons for each solution were weighed, research was done, and analysis was performed. The following pages for the frame, drivetrain, and fairing subsystems recall most of the current decisions that were already made.
​
Keeping all these objectives in mind, a final design for the 2017-2018 KK4OKA Team was created. The following tabs for Our Vehicle go over the individual subsystems and the steps they took to get this finalized version of our vehicle.

Figure 1: The current KK4OKA HPV design