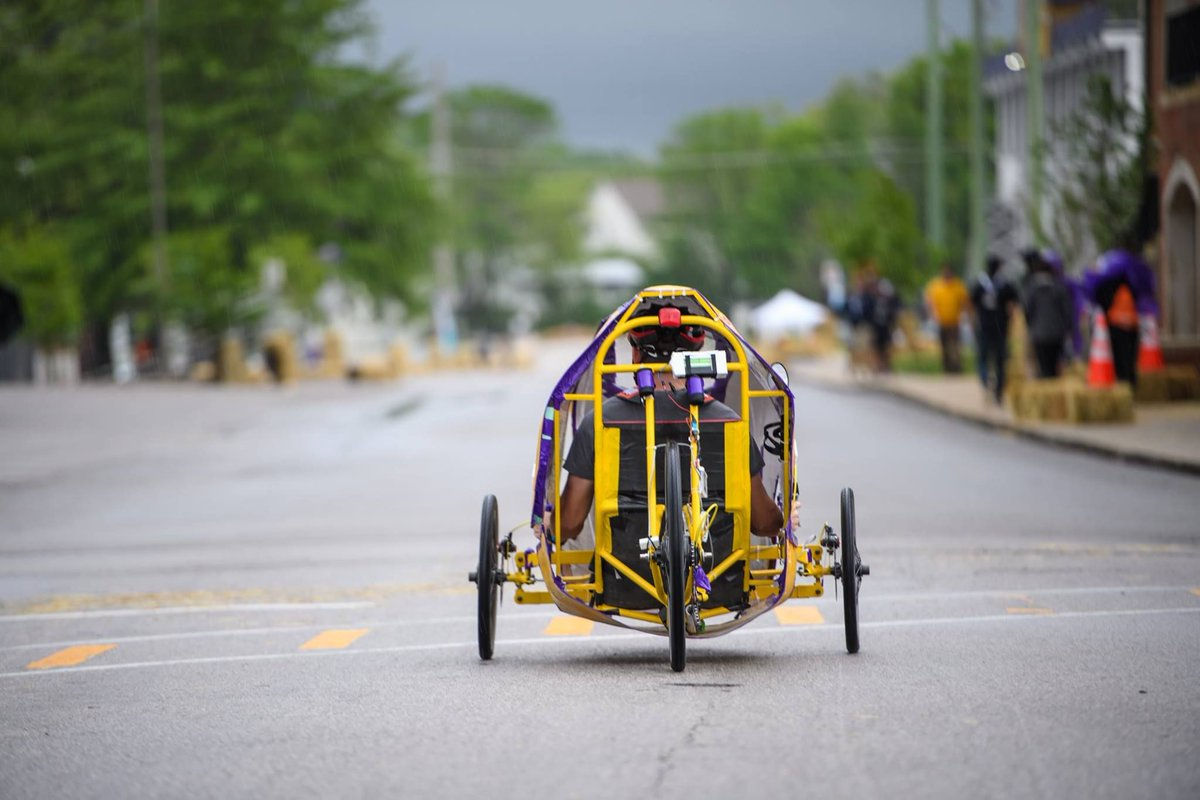
The Drivetrain
The drivetrain is responsible for translating human energy into mechanical motion. It is separated into three micro-subsystems: gearing, steering, and braking. It is the drivetrain's main objective to enable the rider to provide efficient power to the drive wheels. Simultaneously, the drivetrain must allow them to slow down and maneuver the tricycle with ease.
The Steering
The Design Process
The choice of the steering was based heavily on the current system implemented by the previous team, indirect steering, which restricted the turn radius and lacked the ability to clear the frame. Though this type of steering was reconsidered for this year, the other options of pivot steering and direct steering far outweighed it with their benefits. Figure 1 shows some design sketches of the steering systems considered when first conceptualized.
Certain considerations had to be made when choosing the steering system we would implement into our vehicle. Some of these consideration include:
-
Safety — As the main link between the driver's power and the vehicles motion, the steering's safety was ranked as one of the highest criteria
-
Efficiency of the steering — Stemming from the fact that the indirect steering could not clear the vehicle frame, thus making it inefficient, this category was ranked as one of the higher ones for the steering criteria
-
Maintenance — In case of steering failures, a system that is easy to fix and maintain would be ideal
-
Cost of the system — Due to a limited budget, a steering system that would be both cost efficient and manageable was high on the priority list
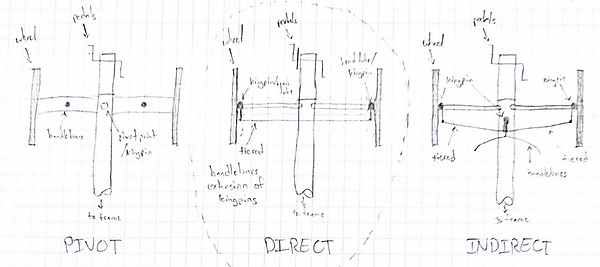
Figure 1: Initial design concepts for the HPV steering

Figure 2: 2016-2017 indirect steering system used
Direct steering outweighed the indirect and pivoting steering without producing any heavy drawbacks. As such, it became the obvious choice as our steering system for the vehicle. With its handlebars above the seat, rather than below it, direct steering won over the other types of steering with its overall efficiency. This was one of the main concerns for steering, as we did not want a repeat of last year where the frame interfered with the steering's turning radius. The ease of using the steering also helped direct steering to win, as it is much simpler with its stationary positioning rather than the rotating axle that is utilized in the pivot steering system.
Figure 3: Current design for the HPV direct steering
The Crankset
As the part of the drivetrain that would allow the rider's leg motion to turn into rotational motion of the vehicle, the crankset was the next main part that had to be decided on. Three types of cranksets were researched; the single chainring, dual chainring, and internally geared crankset.
As with the steering, certain considerations were made when deciding which crankset to use for the vehicle. Some of these considerations include:
-
Efficiency of the crankset — This was weighed heavier due to the requirement to generate movement from the vehicle during the initial gears
-
Safety — This category was also weighed heavily in terms of the crankset's ability for shifting
-
Cost — As manufacturing our own crankset would be difficult, one that was cost efficient while also holding up to our standards of performance was needed

Figure 4: Example of an Efneo Gearbox on a bicycle
Taking the requirements for the crankset into consideration, the internally geared Efneo gearbox became the best choice for the team's vehicle. This gearbox displayed the benefits of not requiring movement while shifting and preventing chain derail, not requiring a tensioner for different gears, and enclosing gears from the environment.
The Brake Setup
The braking system presented the least concern for this year, as the past three "Ke Koa" teams have all used front disc brakes only. Research done has shown that utilizing front brakes, or at least a front bias, is the most efficient way of braking. This is due to the fact that the weight of the vehicle is transferred to the front while braking, rendering rear brakes less useful. While adding rear brakes would be useful in cases of front brake failure or on slippery roads, it would also add to the overall cost and maintenance of the system. While deciding on a brake setup, the use of front disc brakes only, a front and rear wheel brake, and an anti-lock brake system were considered.
The considerations taken into account while choosing a brake setup were similar to that of the steering and crankset criteria. Some of these considerations include:
-
Efficiency of the brake — As previously stated, a front disc brake system has been proven to be efficient by both research and past teams
-
Safety — More emphasis was placed on this category, as without an efficient and safe brake system, the rider would have no way to come to a complete and quick stop without some element of danger
With a heavy emphasis on safety and cost being the highest factors taken into account when choosing the brake setup, it was decided that continuing the use of front disc brakes only would be the best decision for the team. While not the most efficient setup looked into, it would not require a complete conversion from disc to wheel brakes, saving the drivetrain subsystem a lot of time during the manufacturing process.
What's Next?
The current designs listed are up to date with the drivetrain subsystem. While these designs are locked into place, some concerns have been brought to attention in regards to the eventual manufacturing and testing phase of the project. Currently, the drivetrain subsystem is looking into ways to incorporate the vehicle's folding innovation while simultaneously maintaining chain tension. One proposed idea is to have an intermediary tension sprocket attached to two independent chains. Other concerns for the drivetrain subsystem include the vehicle's stability at higher speeds and the exact positioning of the steering due to different rider arm lengths.


Figure 5: Current crankset model for the vehicle
The Manufacturing Process
...coming soon...
